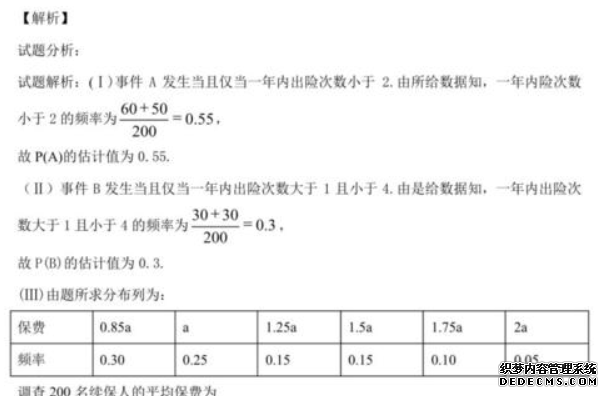
简述凹印油墨在印刷中的常见问题及解决方法
一、色差
1. 原因:原墨色相不一致
2. 处理方法:油墨使用前应检查油墨色相
二、咬色(析出)
1. 原因:油墨中树脂溶解性太好,使用油墨容易再溶解。
2. 处理方法:前一色使用快干溶剂,天富集团 提高前一色的干燥速度,向该色组版面吹风,更换油墨。
三、气泡
1.原因:油墨表面张力太大,油墨黏度不适合。
2.解决方法:保持油墨核实的黏度;添加专用消泡剂,但消泡剂会对油墨性质产生不良影响,使用不当反而会引起气泡,故慎用。
四、油墨面发花
1.原因:印刷时油墨黏度过低、油墨本身的树脂不良、天富代理商 印版滚筒网纹太深;溶剂配比不适合,溶解力差。
2.解决方法:适当提高油墨黏度;使用冲淡剂,以较高速度生产;添加一定的分散剂,提高树脂分散性;调整溶剂配比。
五、印品光泽不足:墨层发暗,光泽性差
1.原因:树脂含量不足;颜料或添加剂粒度粗糙;用无相容性的树脂时。
2.解决方法:添加调金油;尽量细化颜料及添加剂;更换树脂。
六、印版在复合镀铝膜后出现小白点
白点在干式复合中是一个常见故障,除了在符合工艺上解决外,印刷质量也会对此有很大影响,严重时即使调整符合工艺也无法彻底消除。
1.原因:墨层遮盖力不够。
2.解决方法:检验墨层遮盖力应符合要求;调整油墨黏度增加上墨量。
七、白化现象
1.溶剂白化
原因:这种白化现象多见于醇性油墨,当湿度高时,由于溶剂的蒸发潜热现象,印墨皮膜附近会被冷却,使水滴混入其中,造成印墨皮膜白化。当然使用蒸发潜热高的溶剂时,这种现象更容易出现。
解决方法:降低湿度;降低印刷速度;进行印刷的同时,进行加热干燥。
2.树脂白化
原因:当油墨中溶剂平衡性差,真溶剂先挥发,而稀释剂残存在油墨中时,会使印墨之中的树脂析出沉淀,引起白化现象。
解决方法:更换印墨,或者添加一些蒸发速度较慢的真溶剂,更换溶剂配方。
简述凹印专色墨的调配方法
1.根据工艺配比准备好配墨所需油墨,核对油墨的品牌、型号与工艺要求一致,不同厂家,不同品牌的油墨严禁混用,需要混合不同品种的油墨必须事先确认。
2.准备好洁净墨桶。
3.为防止油墨沉淀和分层,油墨在称重前要充分摇动,整桶需倒置摇晃2分钟左右。必本着少量、多次的原则进行,不允许一次性大量配墨。
4.根据工艺配比调配油墨。调配油墨时慎称量确保准确,称量完毕后混合的油墨要搅拌均匀,防止色差。
5.原墨桶用完后需要加盖封好。
6.油墨稀释时要缓缓夹入溶剂,并且要边加边搅拌,以免破坏油墨的性能,并且用黏度杯调整至适当黏度。
选择油墨时应考虑哪些主要因素
1.承印物
2.印刷条件
3.印刷质量要求
4.印后加工条件
简述凹印油墨的印刷适应性
1.凹印油墨是流动性很耗的稀薄流体,要易于填入印版滚筒网穴内。
2.油墨具有良好的刮刀适性,易于刮墨刀将表面上非图文部分的油墨刮去。
3.油墨具有足够的内聚力,放置印版滚筒高速运转时离心力不平衡。
4.油墨具有良好的转移、叠印性能和良好的黏弹性,即印版滚筒上网穴内油墨易于转移到承印物上和已印刷的前一色油墨上且其图像、文字、线条网点不易铺开放大。
5.转移到承印物上后,具有良好的流平性,以保证形成平滑的墨膜。
6.油墨通过溶剂挥发而迅速干燥,其干燥速度与印刷速度相适应。
7.具有一定的复溶性,以保证网穴内转移部分能重新溶入工作墨中。
简述印版的外观检验方法
用溶剂擦干净印版滚筒表面后进行观察,要求印版滚筒无划痕、锈斑、凹坑等,版面光滑、平整,图文和文字周围没有不需要的网穴,网墙整齐、光洁;确保版辊铬层无露铜、灰雾、发花、粗糙、脱落、起皮、划伤、水渍等,铬层呈银白色,色泽一致。
简述压印辊筒对印刷质量的影响
1.压印滚筒的硬度及均匀性:压印滚筒具有合适的弹性,才能顺利地将印版网穴内的油墨转移出来,只有压印辊硬度均匀,才能保证印版颜色的一致性。否则就容易出现印刷白点,浅网部位印不上,拼版各联色不一致等印刷故障。
2.压印滚筒压力及平衡:压印滚筒压力不足容易出现印刷白点现象。压力过大,则容易产生皱褶或印刷品上有斜纹。压印滚筒两侧压力不平衡,容易引起横向排列的拼版单元颜色不一致、套印不稳定、薄膜起皱等情况。
3.压印滚筒的耐压性:通常薄膜印刷时的印刷压力在150-350kg/m左右,如果发生脱色白点就有必要增加印刷压力。不过用于塑料薄膜印刷的压印滚筒其结构为轻压型,同时考虑到作业的方便性而缺乏耐压性。所以如果加500kg/m以上的印刷压力压印滚筒就可能会发生弯曲。这时,压印滚筒两端受到强压,而中央部就容易出现脱色现象,当然也就会造成套色飘移,这种套印飘移现象在宽幅印刷时较为明显。
4.压印滚筒的溶胀变形:经长期使用后,由于油墨及溶剂影响,滚筒的两端会发生溶胀,这时就需要对滚筒进行研磨,否则该单元的图案与其它单元的图案相比宽度就会缩小,就会产生与过压时相同的弓形状态。为减少油墨及溶剂对滚筒的影响,应注意两点:一是印刷基材与压印滚筒在规格上要配套;二是压印滚筒沾上油墨等杂质后要及时擦干净。
5.压印滚筒研磨加工精度:压印滚筒表面的合成橡胶由于溶剂等作用而发生溶胀变形、划伤时,就需要进行研磨。研磨加工时必须注意放置压印滚筒产生锥度,并使印刷时圆周长能够保持相同。如果有锥度、薄膜就容易起皱,横向套印就容易不稳定。如果圆周长不一致,则纵向套印有容易不稳定。另外,如果压印滚筒的动、静平衡处理过差,也会对印刷的均匀性产生不利影响。
简述凹印刮刀的基本规格及其对凹印质量的影响
刮墨刀的厚度乙班为0.1-0.25mm,刮墨刀太薄,容易被印版滚筒磨损,连续生产受到影响;刮墨刀太厚,刀片的弹性变差,容易生产过程中有刀丝等问题发生。
刮墨刀硬度一般在HV450-HV600。刮墨刀硬度不是越硬越好,而是要根据产品的印数、印版滚筒表面层硬度与厚度进行综合考虑;刮墨刀片的硬度过高会加快印版滚筒的磨损,刮墨刀片的硬度过软则刀片磨损过快,刮墨刀片的硬度要与印版表面硬度相匹配,使印版的耐印数保持在一定的范围内,降低成本,提高生产包装印刷品的质量、效率。
简述密度计的使用方法
参照生产厂商的使用说明书来使用光学密度计。需要指出的是,密度计在使用前,首先要在随机配备的标准白板上校正调零。标准白板是一个较为理想的完全白色的硫酸镁反射表面,密度计调零意味着把密度计调整到标准的低密度值,然后进行全面校正,使密度计的高密度值与黑暗空间密度相等,从而确定密度计的量程范围。
简述凹版印刷品质量评价方法
凹版印刷品质评价一般采取主观评价与客观性评价相结合的方法进行。主观性评价方法主要是目视评价,而客观性评价方法则是通过仪器或工具对印刷品定量分析。
主管性评价主要应用与印刷品外观项目。
客观性评价主要指可量化的技术指标。
简述凹版印刷中影响套准质量的主要因素
一、设备因素:印刷品套印精度在很大程度上取决于设备本身的机械制造精度和所使用的计算机自动控制系统的技术水平,它直接决定了运行的平稳性。
二、套准控制设备:只有套准控制装置正常工作,才能保证印刷套准。
三、工艺及操作条件
1.张力:在印刷过程中,张力变化范围小,套印精度就容易控制反之亦然。
2.印刷压力:压力过大易引起印刷皱褶、印墨斜纹及由此带来的套印问题;印刷压力过小,则易造成脱印,缺墨及由此引起的套准问题。
3.导辊运行情况:如果导辊运动经督查,就会导致薄膜张力无规律变化,从而造成套印不准。
4.印版滚筒:印版的质量好坏对凹版印刷来说至关重要。
5.原材料因素
① 承印基材:印刷基材荷叶边、薄厚不均、边缘不整齐等都会直接造成边缘控制不稳,张力变化进而影响套印精度。
② 印刷油墨:油墨颜色会影响自动套准系统的跟踪令名都,套印标记颜色不同,扫描放大器的反射光线强度也就不同,相应的脉冲高度也就不一样。
6.环境因素:温湿度的急剧变化引起承印材料的变化从而影响套印质量。
版权保护: 本文由 天富平台会员注册开户登录链接 原创,转载请保留链接: http://bhlpbz.com//html/2021/0622/202.html